Clifton Water District Design and Construction Standard Specifications
Last Revised: April 9th, 2025
These Clifton Water District (CWD) Design and Construction Standard Specifications, hereinafter referred to as the “Standards” shall apply whenever any work is performed by private Developers that will impact CWD infrastructure. The intent of these Standards is to provide the minimum criteria for the design and construction of water infrastructure within the CWD service area as well as clarify the process for completing new development and redevelopment projects that include connection to or expansion of the CWD’s water distribution system. These Standards are not intended to be applied blindly to every application and do not absolve the design engineer from the responsibility of evaluating the given situation to ensure that the application of these Standards will result in water infrastructure that safeguards the public’s life, health, and property.
100.1 PROJECT APPROVAL PROCESS
Developments that involve the CWD are typically initiated through either Mesa County or the City of Grand Junction and by following the City or County’s permit review process, the CWD will be integrated into the overall project review. Many of the steps listed below are incorporated in the development process established by Mesa County and the City of Grand Junction.
All water system improvements to the CWD’s water system from the plant up to and including the water meter shall be constructed in accordance with the latest version of the Clifton Water District Standard Specifications or Improvements and as directed by the CWD.
Below is a flow chart showing the steps needed to take a project from the design phase to the completed product.
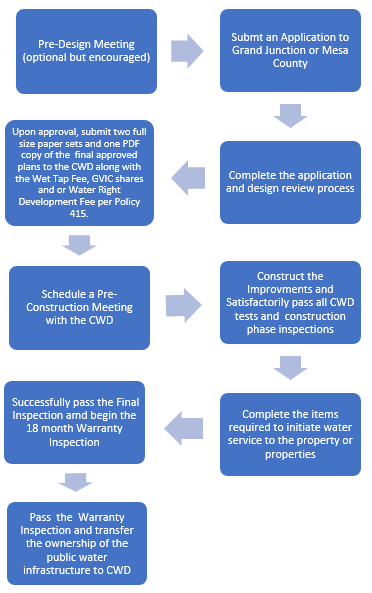
100.1.1 PRE-DESIGN MEETING
A pre-design meeting with the CWD is recommended, but not mandatory to discuss onsite and potential offsite infrastructure improvements required to ensure adequate pressure and flow for the development. The meeting is also an opportunity for the Developer’s team to gain an understanding of the requirements for designing and constructing water system improvements within the CWD.
100.1.2 APPROVAL TO CONSTRUCT WATER SYSTEM IMPROVEMENTS
Prior to the construction of any water system improvements the following must be received and approved by the CWD:
- Contact information for the Developer/Owner, Engineer, Project Coordinator, and Contractor. The contact information shall consist of mailing address, email address, and phone numbers. See New Construction Project Information Sheet.
- Two paper sets and one PDF copy of the final CWD approved construction plans and design calculations signed and sealed by a Colorado licensed Professional Engineer.
- An itemized Engineer’s Opinion of Construction Costs signed and sealed by a Colorado licensed Professional Engineer, or the Contractor’s itemized bid signed by both the contractor and Developer or his designee.
- Executed easement documents (if applicable). Easements shall be in accordance with CWD Standards.
- Payment of the “Wet Tap Fee – Main Line Extension”.
- Transfer of GVIC shares and or payment of fee in lieu of Water Right Development Fee - see CWD Policy 415
100.1.3 EXPIRATION
If construction work has not started within 12 months of plan approval by the CWD, the project shall be considered inactive, and the approval shall expire. The Owner may submit a written request for an additional 12-month time extension. Upon receipt of such request, the CWD may extend the expiration date an additional 12 months if the plans comply with the then current CWD requirements and are consistent with any CWD planning goals. If the CWD determines that the previously approved plans do not comply with the then current requirements, the plans will need to be revised and resubmitted to the CWD for review.
Incomplete project applications shall be considered inactive and shall expire 12 months after the CWD’s latest review comments. After expiration of the project application the project shall be required to comply with the then current requirements.
100.1.4 PRE-CONSTRUCTION MEETING
A pre-construction meeting is required prior to the start of construction of any water system improvements. The developer/contractor must submit a project schedule and a list of subcontractors and material suppliers atleast two business days prior to the pre-construction meeting. This meeting should be held in conjunction with Mesa County or the City of Grand Junction.
100.1.5 CWD INSPECTIONS
District personnel or authorized representatives must be provided access to all work being performed and must be allowed to inspect such work at its convenience. Inspection and testing shall be in accordance with the CWD Standard Specifications for Water System Improvements. Inspections must be scheduled 48 hours in advance.
100.1.6 AS-BUILT DRAWINGS
Prior to initiating water service to any properties, as-built drawings must be submitted to the CWD for approval. The as-built drawings shall consist of a marked up set of original approved construction drawings that clearly shows the original and as-built improvements. The record drawings shall include dimensions, stationing, or coordinates for all service taps, valves, fittings, and fire hydrants. All meter vaults shall be dimensioned from the nearest property corner. As constructed top of pipe elevations shall be provided for any location where the water main elevation varies from the standard 42" depth of bury.
The as-built drawing submittal shall include one full size paper copy and one PDF copy.
100.1.7 INITIATION OF WATER SERVICE
The steps that must be taken prior to initiating water service to individual parcels fall into two categories: work that must first be completed by the Developer/Owner that encompasses the entire subdivision filing; and steps that must be taken by the owner of the individual lot after the subdivision wide requirements have been met.
Requirements of the Developer/Owner of the Subdivision:
i) Successful completion of the water system improvements including passing the required pressure and bacteriological tests.
ii) Receipt of backfill compaction testing.
iii) Receipt of One paper copy and one PDF copy of the approved Record Drawings signed and sealed by a Colorado licensed Professional Engineer.
iv) Receipt of a recorded address plat with tax property identification numbers and addresses for each parcel.
v) Receipt of an itemized final construction cost for the water system signed and dated by the Developer/Owner or contractor.
vi) Receipt of a letter from the Developer/Owner transferring all ownership interests in the water main extension and appurtenances to the CWD.
Requirements of the Owner/builder for the individual lot
i) Receipt of a Mesa County building permit.
ii) Payment of the Tap Fee.
iii) Execution of a Clifton Water District Water Service Agreement.
The CWD shall supply all water meters. Water meters 2” and smaller shall be installed by the CWD. Meters larger than 2” shall be installed by the Owner/Developer’s contractor under the direct onsite supervision of CWD staff.
100.1.8 ACCEPTANCE OF IMPROVEMENTS/EIGHTEEN (18) MONTH WARRANTY
Prior to acceptance of the completed water system improvements by the CWD, and prior to the start of the warranty period, all inspection and testing requirements as per the CWD Standard Specifications for Improvements must be met, and a final inspection performed by the CWD and the Developer/Owner or their representatives.
After the development passes the Final Inspection the 18-month warranty shall commence. The Developer/Owner shall warranty all water system related improvements for a minimum of eighteen months against defective material, workmanship, and faulty design. The Developer/Owner shall be responsible for all maintenance and repair work necessary during the warranty period.
If the Owner/Developer fails to adequately address any maintenance or repairs within an appropriate time frame per notification by the CWD, the CWD reserves the right to perform any work necessary to maintain and or correct these defects or inadequacies. The Developer/Owner shall be responsible for reimbursing the CWD double the cost incurred by the CWD while undertaking any maintenance or corrective actions that the Developer/Owner fails to complete in a timely fashion after notification by the CWD.
The Developer/Owner shall indemnify CWD for and from any claims against the CWD and any damages the CWD may suffer due to defects in materials, workmanship, and inadequate design of the water system improvements or ancillary improvements related to the water system improvements.
100.1.9 OWNERSHIP OF WATER SYSTEM IMPROVEMENTS
The CWD will operate the Water System Improvements up to and including the meter and meter vault as of the date of acceptance of the improvements. The CWD will accept full ownership of said improvements at the end of the eighteen (18) month warranty subject to the following:
i) Satisfactory passing of the Warranty Inspection. The Warranty Inspection is to be performed by or immediately prior to the end of the warranty period. If any portion of the Water System Improvements are found to be defective and/or inadequate in any way and for any reason during the Warranty Inspection the warranty period shall be extended until the defects and/or inadequacies are remedied by the Developer/Owner to the satisfaction of the CWD.
ii) Water System Public Improvements Ownership Transfer signed by the Developer/Owner.
100.2 APPLICABLE CODES, STANDARDS, AND SPECIFICATIONS
All design, materials, and construction shall be in accordance with these Standards and all applicable governmental, regulatory, and testing organizations including, but not limited to the following:
i) Colorado Department of Public Health and Environment (CDPHE)
ii) All CWD Policies, Procedures, and Resolutions.
iii) Colorado Department of Transportation Standard Specifications for Road and Bridge Construction
iv) Mesa County
v) City of Grand Junction
vi) USEPA Recommended Standards for Water Works
vii) Recommended Standards for Water Works – 10 State Standards
viii) American Water Works Association (AWWA)
ix) American Society of Testing and Materials (ASTM)
x) American National Standards Institute (ANSI)
Whenever a provision of these Standards or any provision in any law, ordinance, resolution, rule or regulation of any kind, contains any restrictions covering any of the same subject matter, whichever standard is most stringent shall apply.
100.3 LEGAL RELATIONS AND RESPONSIBILITIES
The Developer/Contractor shall always comply with all Federal and State laws, local laws and ordinances, and any regulations which in any manner affect the project. The contractor shall release, indemnify and promise to defend and save harmless the CWD, its officers, employees and agents from and against any and all liability, loss, damage, and expense, actions and claims, including costs and reasonable attorneys’ fees incurred by the CWD in defense thereof, asserting or arising directly or indirectly on account of any violation of laws, ordinances or regulations whether such violations are by the contractor, his or her subcontractors, his or her employees, or his or her agents.
100.4 SEVERABILITY
If any section or article of these Standards is found to be unconstitutional or illegal by any court, the said section or article shall have no bearing on the effectiveness of the rest of these Standards.
100.5 VARIANCES
The CWD may vary the Standards on a case-by-case basis if it is determined that such variances are in the best interest of the CWD. Any modifications that do not conform with CDPHE requirements shall not be allowed. Variance requests must include proof that compliance with the Standards cannot be accomplished and that the proposed variance will not diminish the operational or structural integrity, or maintainability of the improvements. Variance requests must be based on sound engineering principles and judgement.
100.6 CONSTRUCTION PLANS AND DESIGN CALCULATIONS
Construction plans must be signed, sealed and dated by a Colorado licensed Professional Engineer and shall at a minimum include and or adhere to the following:
i) All water infrastructure improvements including fire hydrants, valves, service connections meter pits and fittings.
ii) Water main plan and profile views showing all vertical conflicts with any potential sources of contamination such as sewers, drain lines, raw water lines, and irrigation lines.
iii) All water mains shall be a minimum of 8” diameter and shall be looped whenever possible. Dead end mains shall terminate at a fire hydrant.
iv) All water services shall be individually tapped from a public main.
v) Only one CWD water meter shall be connected to each water service.
vi) Each CWD meter shall only serve a single parcel
vii) Dimensions between the proposed watermain and sources of potential contamination.
viii) Dimensions to the top of the proposed watermain including dimensions for areas where the watermain is proposed to be installed lower than the CWD standard.
ix) All applicable CWD Standard Details.
x) CWD approval block on each water related plan sheet.
Design Calculations shall be submitted for all non-residential domestic water services in accordance with AWWA M22.
100.6 EASEMENTS
Whenever water mains are not located in the public right of way or in a Mesa County or City of Grand Junction multi-purpose easement, a permanent easement shall be granted to the CWD. Watermains 12” in diameter and less shall be in the center of a minimum 20-foot-wide permanent easement. Permanent structures with fixed foundations such as houses and garages shall be set back a minimum of 15 feet from the centerline of all water mains located within easements.
Language for easements to be granted to the benefit of the CWD must be approved by the CWD.
101.1 GENERAL
This section covers pipe and other materials to be used in the construction of potable water systems. All materials used shall be new and in conformance with the applicable standards.
101.2 CONTRACTOR REQUIREMENTS
All materials to be furnished by the Contractor shall conform to the requirements of these specifications. The type, size and strength class of pipe, fittings and other materials shall be as shown on individual project plans or otherwise specified in the Contract Documents.
101.3 CWD FURNISHED MATERIALS
When CWD furnishes materials that are to be incorporated into the work by the Contractor, provisions will be made in the Special Conditions as to the responsibilities of CWD and the Contractor regarding delivery, unloading, and storage of the materials.
101.4 INSPECTION AND TESTING
All pipe shall be tested in conformance with the applicable standards. Testing may be witnessed by CWD’s representative, or by an approved independent testing laboratory. Upon request of CWD, the Contractor shall provide a copy of certified test reports indicating that the material conforms to the applicable specifications.
101.5 HANDLING
All materials shall be handled with equipment and methods adequate to prevent shock or damage. Under no circumstances shall materials be dropped. Pipe handled on skidways shall not be skidded or rolled against pipe already on the ground.
If any part of the coating or lining is damaged, the Contractor shall repair or replace the material at Contractor’s expense as directed by CWD. All pipe and appurtenances shall be handled in accordance with the appropriate AWWA and ASTM standards.
101.6 STORAGE
The Contractor will be held responsible for the safe storage and protection of all pipe and other materials delivered to the work site. The interiors of all pipe and fittings shall be always kept free from dirt and foreign matter. Gaskets for pipe joints shall be stored in a cool location out of direct sunlight. Any material that has been damaged shall be repaired or replaced at the Contractor’s expense.
101.7 PIPE AND FITTINGS FOR WATER MAINS AND SERVICE CONNECTIONS
101.7.1 DUCTILE IRON PIPE
Ductile iron pipe shall be single gasket, double sealing pipe per AWWA C151/ANSI A21.51 with cement mortar lining per AWWA C104/ANSI 21.4. The exterior of the ductile iron pipe shall be coated with arc-sprayed zinc at a mass to surface rate of 200 g/m2. The zinc coating shall meet ISO 8179. A bituminous top- coat shall be provided over the zinc coating. The pipe shall conform to AWWA C-151, thickness-class to be determined in accordance with AWWA C-150 and shall be a minimum of Class 52.
101.7.2 JOINTS
Unless otherwise specified in the Construction Plans or Special Conditions, ductile iron pipe joints shall be mechanical or push on joints conforming to AWWA C-111/A21.11. Gaskets shall be of neoprene or other synthetic rubber material. Nitrile Rubber (Acrylonitrile Butadiene) shall be used if hydrocarbons or petroleum is present in the soil. All push-on-type joints shall be electrically connected with brass wedges or cadweld connectors and No. 12 copper wire.
101.7.3 POLYETHYLENE ENCASEMENT
Polyethylene encasement material in conformance with AWWA C600 and AWWA/ C-105/A21.5.
101.7.4 POLYVINYL CHLORIDE PIPE (PVC)
PVC pipe 4” in diameter and larger shall conform to AWWA C900. Unless otherwise specified the minimum thickness class of pipe where the operating pressure is less than or equal to 120 psi shall have a Dimension Ratio (DR) of 18. Depending on local conditions and in areas where the operating pressures are greater than 120 psi, the CWD may require the design engineer to verify the PVC Pressure Class and DR required for the specific application in accordance with AWWA M23.
Joints: Unless restraining is required joints shall be bell and spigot push on type in conformance with ASTM D3139. The bell shall consist of an integral wall section with factory installed flexible elastomeric gaskets that conform to ASTM F477. The bell shall be at least as hydrostatically strong as the pipe wall. In normal soil conditions gaskets shall be made from Styrene Butadiene Rubber. Nitrile Rubber (Acrylonitrile Butadiene) shall be used if hydrocarbons or petroleum is present in the soil.
PVC pipe for use in underground main line boring projects or when installed in casing pipes attached to bridges shall be either “Certa-Lok” or “Yelomine” as manufactured by CertainTeed Corporation, no substitutions allowed. “Certa-Lok” C900/RJ PVC pipe shall meet all the requirements of AWWA C900 “Polyvinyl Chloride (PVC) Water Distribution”. The pipe shall be joined using separate couplings that have beveled edges, built-in sealing gaskets, and restraining grooves. The restraining splines shall be square and made from Nylon 101. “Yelomine” PVC pipe shall meet all the requirements of ASTM D2241, “Standard Specification for PVC Pressure-Rated Pipe (SDR Series)”. The pipe shall be joined using separate couplings that have beveled edges, built-in sealing gaskets, and restraining grooves. The restraining splines shall be square and made form Nylon 101. Each pipe and coupling shall be approved by the National Sanitation Foundation for use with potable water.
PVC plastic pipe for lines 1-1/2- inch (1-1/2") Through three-inch (3") diameter shall conform to ASTM D2241. Unless otherwise specified, the minimum thickness class of PVC 1-1/2" through 3" diameter shall conform to SDR 21 (Class 200), and shall be joined with SOLVENT WELD bushings, collars, couplings, tees, and bend fittings equal in diameter and pressure classification to the pipe.
The Contractor and/or Pipe Manufacturer shall follow the standards listed below, except as otherwise specified herein. The latest revision or edition in effect at the time plan approval shall be utilized.
A. American Society for Testing and Materials (ASTM)
- D1784 – Standard Specification for Rigid Poly(Vinyl Chloride) (PVC) Compounds and Chlorinated Poly(Vinyl Chloride) (CPVC) Compounds
- D2241 – Polyvinyl Chloride (PVC) Pressure-Rated Pipe (SDR PR Series)
- D2774 – Practice for Underground Installation of Thermoplastic Pressure Piping
- D3139 – Joints for Plastic Pressure Pipes Using Flexible Elastomeric Seals
- F477 – Elastomeric Seals (Gaskets) for Joining Plastic Pipe
B. American Water Works Association (AWWA)
- C605 – Underground Installation of Polyvinyl Chloride (PVC) Pressure Pipe and Fittings for Water
- C651 – Disinfecting Water Mains
- C900 – Polyvinyl Chloride (PVC) Pressure Pipe and Fabricated Fittings, 4 in. through 60 in. (100 mm through 1500 mm), for Water Transmission and Distribution
- M23 – PVC Pipe – Design and Installation
C. National Science Foundation (NSF)
- 61 – Drinking Water System Components – Health Effects
D. Uni-Bell PVC Pipe Association
- UNI-PUB-8 – Tapping Guide for PVC Pressure Pipe
- UNI-PUB-9 – Installation of PVC Pressure Pipe
- Handbook of PVC Pipe Design and Construction
101.7.5 COPPER SERVICE PIPE
Copper tube for water service lines 1” and smaller shall be Type K, soft temper, for underground service conforming to ASTM B-88 and B-251. The pipe shall be marked with the manufacturer’s name or trademark and a mark indicating the type of pipe. The outside diameter of the pipe and minimum weight per foot shall not be less than that listed in ASTM B-251, Table II. All fittings on copper service lines shall be brass compression type as manufactured by Mueller Company, A.Y. McDonald, or Ford Company.
101.7.6 MECHANICAL RESTRAINED PIPE JOINTS
Exterior pipe joint restraints for 4 inch through 12-inch C900 PVC pipe with bell and spigot push on joints shall be Series 1900 Split Serrated Restraint Harness as manufactured by EBAA Iron or approved equal. Exterior pipe joint restraints for 14 inch through 54-inch C900 PVC pipe with bell and spigot push on joints shall be Series 2800 Megalug Restraint Harness for new installations or Series 1100HV Split Restraint Harness for existing bell and spigot push on joints, as manufactured by EBAA Iron or approved equal.
Exterior pipe joint restraints for new installation of ductile iron pipe push on bell joints shall be Series 1700 Megalug Restraint Harness as manufactured by EBAA Iron or approved equal. Exterior pipe joint restraints for existing ductile iron pipe push on bell joints shall be Series 1100HD Split Megalug Restraint Harness as manufactured by EBAA Iron or approved equal.
101.7.7 FITTINGS
Fittings for ductile iron pipe and 4" diameter or larger PVC pipe shall be cement lined, Bituminous coated ductile iron with Megalug mechanical joints as manufactured by EBAA Iron or equal in accordance with AWWA C-111 and shall have a minimum pressure rating 250 psi, but not less than that specified for the pipe. All ductile iron pipe fittings shall be produced in accordance with all applicable terms and provisions of AWWA C104-08, AWWA/ANSI C110/A21.10, ANSI/AWWA C153/A21.53 and ANSI/AWWA C111/A21.11 as manufactured by Tyler Pipe, no exceptions.
101.7.8 STEEL CASING
Pipe shall be smooth-walled, welded steel pipe fabricated in conformance with ASTM A36 plate or ASTM A1011 sheet with a minimum yield point of 248 MPa (36,000 psi), conforming to AWWA C200.
Internal Coating: Coal tar epoxy coating per ANSI-A21.4 and AWWA C104 minimum 16 mils dry film thickness.
External Coating for above ground applications: Above ground steel casing shall be coated with a 3-coat epoxy/epoxy/polyurethane system in accordance with AWWA C-218, “Coating the Exterior of Aboveground Steel Water Pipelines and Fittings,” Section 2.5, Coating System No. 4-91
• Prime Coat: 2-component, pigmented, catalyzed Polyamide epoxy; DFT of 3-4 mils.
• Intermediate Coat: 2-component, catalyzed Polyamide epoxy; DFT of 4-6 mils.
• Finish Coat: 2-component aliphatic polyurethane; DFT 3-4 mils. Ensure the total system has a minimum DFT of 10 mils.
External Coating for below ground applications: Coal tar epoxy coating per ANSI-A21.4 and AWWA C104 minimum 16 mils dry film thickness.
Table 101.1 Minimum Casing Dimensions
Carrier Pipe Diameter (inches) | Minimum Casing Inside Diameter (inches) | Wall Thickness (inches) Under Highways | Wall Thickness (inches) Under Railroads |
---|---|---|---|
6 | 14 | 0.25 | 0.375 |
8 | 16 | 0.25 | 0.375 |
10 | 18 | 0.312 | 0.375 |
12 | 22 | 0.312 | 0.375 |
14 | 27 | 0.375 | 0.438 |
16 | 30 | 0.375 | 0.5 |
18 | 32 | 0.375 | 0.5 |
20 | 34 | 0.375 | 0.563 |
24 | 40 | 0.5 | 0.625 |
30 | 45 | 0.5 | 0.625 |
101.7.1 CASING SPACERS AND END SEALS
Casing spacer shall be a two-piece shell per carrier pipe and made from T-304 stainless steel of a minimum 14-gauge thickness. Each shell section shall be lined with a 0.090” thick, ribbed PVC extrusion with a retaining section that overlaps the edges of the shell and prevents slippage. Bearing surfaces (runners) shall be ultra-high molecular weight polyethylene (UHMW) to provide abrasion resistance and a low coefficient of friction (0.12). The runners shall be attached to support structures at appropriate positions to properly support the carrier pipe within the casing pipe and to ease installation. The runners shall be mechanically bolted to the spacer. Risers shall be made of T-304 stainless steel of a maximum 10 gauge and the bolt heads are welded to the inside of the risers for strength. When applicable, all risers shall be MIG welded to the shell. Bottom risers 6” and over in height shall be reinforced. All reinforcing plates shall be 10 ga. T-304 stainless steel and shall be MIG welded to mating parts.
The carrier pipe shall be centered & restrained within the casing pipe and the spacer shall be sized such that the height of the risers and runners are to center the carrier pipe in the casing pipe with a top clearance of three-fourths inch minimum.
Casing spacers shall be Style CSS as manufactured by Cascade Waterworks or approved equal. Casing spacers shall be placed a maximum of 2’ from either end of the casing pipe and at intervals along the carrier pipe no greater than 6 feet.
End seals shall be Neoprene with T-304 stainless steel bands Style CCES Casing End Seal as manufactured by Cascade Water Works or approve equal.
101.8 APPURTENANCES FOR WATER DISTRIBUTION
101.8.1 FIRE HYDRANTS
Fire hydrants shall be the dry bowl type and shall conform to requirements of AWWA C-502. The standard hydrant shall have a six-inch connection, a 5 ¼-inch main valve opening, two (2) 2 ½-inch hose nozzles and one (1) 4 ½-inch pumper nozzle. The hydrant barrel shall be marked with a circumferential rib to denote the intended ground line. The centers of the hose nozzles and pumper nozzle shall be 18” to 22” above finish grade.
Hydrants shall be of the “traffic” or “breakaway” design, having easily replaceable breaking devices for the grade line flange and operating stem that prevents damage to the barrel sections upon impact.
The operating nut and nozzle cap wrench nuts shall be 1 3/8-inch pentagon, measured from point to opposite flat side at the base. The height of the nut shall not be less than one inch.
The nozzle caps shall be removed and the operating nut opened by turning to the left (counter-clockwise). Nozzle caps shall be securely chained to the upper barrel section.
Fire hydrants shall be either Mueller Model A-423 Super Centurion 250 or Kennedy K81-D 3-way hydrant. Hydrant shall meet the applicable requirements of ANSI/AWWA C502 Standard and UL 246 and FM 1510 specifications.
The 2 ½-inch hose nozzles shall be National Standard fire hose thread and the pumper nozzle shall be National Standard 4 ½ -inch.
PAINTING: All fire hydrants shall be painted “factory” red.
101.8.2 GATE VALVES
All valves 12” in diameter and less shall be resilient wedge gate valves and shall meet or exceed all applicable requirements of ANSI/AWWA C515 and AWWA C111, UL 262 listed and FM 1120/1130 approved and certified to ANSI/NSF 61 and 372. Mechanical joint ends shall comply with ANSAIO/AWWA C111. All 3” and larger gate valves shall be Mueller RW Series A-2361 or American Flow Control Series 2500, 350 psi working pressure, or approved equal with either MJ or flanged connections depending on the application. All 2” gate valves shall be American Flow Control Series 2500 or Mueller RW Series 2362, 250 PSI working pressure with threaded connections, or approved equal.
All gate valves shall open left (counterclockwise), be double disc, cast iron body, fully bronze mounted with non-rising stem and parallel seats. The stem and all wearing surface shall be bronze or other approved non-corrosive material. Contact surfaces shall be machine finished and all wearing surfaces shall be easily renewable. Nonferrous bushings shall be of substantial thickness, tightly fitted and pressed into machined seats. Solid wedge valves are not acceptable. Bonnet and stuffing bolts shall be stainless steel.
The valve shall be epoxy coated. The coating shall meet or exceed the requirements of ANSI/AWWA C550 standard.
101.8.3 WRENCH NUTS
Wrench nuts shall be made of cast iron and shall be 1 5/16-inches square at the top, 2 inches square at the base and 1 3/4-inches high.
101.8.4 TAPPING VALVES
All tapping valves shall be resilient wedge with M.J. X FL ends and shall meet or exceed the applicable requirements of ANSI/AWWA C515 Standard, UL 262 listed, FM 1120/1130 approved and certified to ANSI/NSF 61 and 372. Tapping valves shall be either American Flow Control Series 2500 RW or Mueller T-2361 Resilient Wedge Tapping Valves with a minimum working pressure of 350 psi or approved equal.
101.8.5 BUTTERFLY VALVES
All valves greater than 12” shall be butterfly Valves conforming to ANSI/AWWA C-504 standard Class 250B, NSF 61/372 certified, and rated for a minimum working pressure of 350 psi. The butterfly valve shall be a Lineseal 350 as manufactured by Mueller or approved equal.
101.8.6 VALVE BOXES
All valve boxes shall be produced with Class 35 cast iron in accordance with ASTM A48 and shall be 5 1/4-inch diameter, slip type sized for the type of valve and depth of bury. The lid shall have the word “WATER” permanently cast on the top.
101.8.7 AIR VALVES
Air valves shall be of the type, class, and size specified. A separate isolation valve of the same size and pressure rating as the air valve shall be installed between the water main and the air valve. Each air valve shall be housed in a vault made of reinforced concrete pipe or manhole riser section. The vault shall be covered with a precast concrete lid and cast-iron manhole ring and perforated cover. The total area of perforations in the manhole cover shall be as detailed on the plans or specified by CWD.
101.8.8 ELECTRICAL TRACING WIRE
Electrical tracing wire shall be size No.10, solid copper, insulated wire. The insulation shall be blue.
101.8.9 CORPORATION STOPS AND TAPPING SADDLES
Corporation stops shall be made of brass and in conformance with ANSI/AWWA C800. The corporation stop shall be the same size as the service line (3/4 inch and 1 inch only) in conformance with AWWA /CC Tap Thread, the outlet of the stop shall be a compression end for use with type K copper service tubing. Saddles shall be compatible with C900 PVC pipe and CC tapped. Acceptable manufacturers are Mueller Company, Ford Company, or A.Y. McDonald.
101.8.10 METER YOKE ASSEMBLIES
Meter yokes (3/4" x 5/8" or 1" size) shall be factory fabricated with compression connections to service lines, dual check, copper and brass, with stabilizers and ball valves. All meter valves shall be provided with a locking device and meter coupling attached. Yokes shall be as manufactured by Mueller Company or Ford Company. All meter yoke assemblies greater than 1" in size require CWD approval and will require a bypass and accessible vault for containment.
Meter pits shall be 20" inside diameter, 32" in height with preformed service line pipe access. Pits shall be double-walled plastic round meter box type as manufactured by Mid-States Plastics, Inc. Meter pit bells and lids shall be cast iron with the pentagon locking nut lid as manufactured by Castings, Inc. and shall be pre-drilled for AMI radio attachment.
101.8.11 REDUCED PRESSURE BACKFLOW PREVENTION DEVICES
Reduced pressure backflow prevention devices shall be the same as the service line and shall be approved by the Foundation of Cross-Connection Control and Hydraulic Research at the University of Southern California.
101.8.12 CONCRETE AND MORTAR
All concrete used in construction of manholes, inlet boxes, vaults, concrete encasement, thrust blocks, etc., shall be Colorado Division of Highways “Class B.” Unless otherwise specified, all mortar shall be Type M in accordance with ASTM C 270.
101.8.13 BOLTS
All M.J. and Flange Bolts shall be Cor-Blue Bolts or approved equal. All packing box bolts on gate valves or butterfly valves shall be grade 304 stainless steel bolts with Grade 316 stainless steel nuts.
101.8.14 PIPE INSULATION
Acceptable pipe insulation products include two-pound spray polyurethane foam, extruded polystyrene foam, and polyurea encapsulated close-cell foam pipe insulation as manufactured by Dragon Jacket or approved equal. Pipe insulation shall have a minimum “R” value of 8.
101.8.15 SAMPLE STATIONS
The contractor installed water quality sample stations shall be as manufactured by Kupferle Model Eclipse 88.
102.1 DESCRIPTION
This section covers surface removals, excavation, backfilling, compaction, disposal of surplus material, restoration of disturbed surfaces, and all other work required for the safe and proper construction of potable water systems.
102.2 SURVEY LINE AND GRADE
Unless otherwise specified, a registered Engineer or a Registered Land Surveyor registered in the State of Colorado or someone under their supervision will set line and grade control hubs or pavement markings for piping at a maximum spacing of one hundred (100) feet. A greater interval may be used in conjunction with the use of a laser instrument for maintaining line and grade. Center line location and grade for fittings, valves, fire hydrants, service connections, meter pits, and other appurtenances shall be established by setting two control hubs or pavement markings for each item.
102.3 SURFACE REMOVALS AND TOPSOIL PRESERVATION
The Contractor shall remove surface materials and obstructions only to the widths necessary for excavation of the trench. All trees, shrubbery, fences, and other plantings and structures not designated for removal shall be protected or, if moved, restored to their original condition after construction is complete.
Removal of concrete curbs, gutters, sidewalks, driveways, and asphalt pavement shall be along existing joints or neatly cut lines. All vegetation, concrete, asphalt, and other refuse removed from the construction limits shall be separated from suitable topsoil and backfill material and hauled to an authorized disposal site secured by the Contractor.
Where the trench is in an unpaved area, clean topsoil suitable for final grading shall be stripped, stockpiled separately in approved locations, and restored to the surface after the trench is backfilled.
102.4 BRACING AND SHEETING OF TRENCHES
When necessary or required, trenches shall be properly braced, sheeted or otherwise supported to provide safe working conditions and protection of the work and adjacent property.
All bracing, sheeting, trench shields, and trench boxes shall conform to the recommendations in the Occupational Safety and Health Administration Standards for Construction (OSHA). Unless otherwise approved, all trench support materials shall be removed in a manner that will prevent caving of the sides and
movement or other damage to the pipe.
102.5 TRENCHES WITH SLOPING SIDES
Where working conditions and right of way permit trenches may be excavated with sloping sides in conformance with OSHA standards with the following limitations:
(1) In traveled streets, alleys, or narrow easements, only vertical trenches with proper bracing will be allowed.
(2) All soils shall assumed to be OSHA Type C soil, unless otherwise classified by a qualified soils technician.
(3) Where trenches with sloping sides are permitted, the slopes shall not extend below a point 12 inches above the top of pipe. The trench shall be excavated with the vertical sides below this point with widths not exceeding those specified on the Standard Detail Sheets.
102.6 Open Excavation Limits
The length of open trench shall be kept to a minimum and shall not exceed the length necessary to accommodate pipe laying and backfilling operations unless otherwise approved by the Engineer. The Contractor shall be responsible for covering or barricading unattended trenches and excavations as necessary for protection of the public and the work. All trenches and excavations shall be backfilled at the end of each workday, unless otherwise shown on the plans or approved by the Engineer. The end of a trench may be left open overnight if the entire perimeter of the excavation is fenced, lighted and barricaded with construction equipment and/or Jersey barriers. No traffic lane shall be blocked by an open excavation, piece of equipment or other obstruction without a proper lane closure, road closure or other approved traffic control.
102.7 Unauthorized Excavation and Pavement Removal
Unless authorized by the Engineer, all removed pavement and excavations made beyond the lines and grades shown on the Construction Drawings or described in the Contract Documents shall be replaced at the Contractor’s expense.
102.8 UNSTABLE TRENCH BOTTOM
Where the excavation is found to consist of muck, organic matter, or any other material that CWD determines to be unsuitable for supporting the pipe, the Developer/Owner’s Engineer shall be required to evaluate the suitability of the native soils to support the proposed improvements and shall provide recommendations for constructing a stable base for the proposed improvements.
102.9 BEDDING AND SHAPING TRENCH BOTTOM
Unless otherwise specified in the Special Conditions, or directed by the CWD in the field, all trenches shall be excavated to at least four (4) inches below the pipe grade and brought back to grade with approved bedding material. The bedding material shall be hand shaped and graded until the trench bottom is uniform and free from rocks, bumps, and depressions. A coupling or bell hole shall be dug at each pipe joint with sufficient length, width and depth to permit assembly of the joint.
102.10 Cutoff Walls
Cutoff walls shall be installed along every utility line to inhibit the movement of ground water through the screened rock bedding. Cutoff walls shall be 5 to 10 feet long and consist of native material or imported material that has a permeability rate the same or less than that of the native material. Cutoff walls shall be constructed by discontinuing the installation of bedding and haunch backfill material and installing approved native or imported material. Cutoff walls shall be installed at intervals not exceeding 200 feet on pressurized lines.
102.11 Rock Excavation
Rock excavation shall consist of the removal of boulders or concrete measuring one-half (l/2) cubic yard or more of hard shale, sandstone, or other bed rock which, in the opinion of the Engineer, requires for its removal the continuous use of pneumatic tools or drilling and blasting. Rock excavation shall be in accordance with Section 203 of the CDOT Standard Specifications for Road and Bridge Construction.
Before payment for Rock Excavation is approved, the Contractor will be required to demonstrate that the material cannot be removed by hand pick or by power operated excavator weighing no less than 45,000 pounds. No payment will be made for Rock Excavation unless authorized by the Engineer in writing prior to the work being done.
102.12 BLASTING
Whenever rock excavation is encountered, air or hydraulic hammers or some equivalent method will be used if possible. Blasting shall be used only if other methods have proven unsuccessful and only upon approval of all applicable federal, state, and local permitting authorities.
At a minimum the following conditions must be satisfied before blasting will be allowed:
1. One competent experienced person shall be specifically designated in charge of explosives and all related activities. The blaster-in-charge shall carefully supervise all work related to the use, storage, transportation, and handling of explosives. The blaster-in-charge or the Contractor shall select a
blasting crew to assist with explosives activities, including transportation and area security. Only competent, qualified, experienced personnel shall be permitted to handle explosives. Anyone demonstrating carelessness, incompetence, or inexperience shall be excluded from further handling of explosives. The blaster-in- charge shall demonstrate the following minimum qualifications:
a. Proof of a valid Colorado Blaster's License or other license issued by an equivalent licensing body.
b. Written résumé showing not less than three years of active involvement as blaster- in-charge on projects similar in scope to the current project.
c. Five references who can testify to the known qualifications and reliability of the proposed blaster-in-charge.
2. The blasting crewmembers shall demonstrate the following minimum qualifications:
a. Completion of at least 24 hours of explosives and blasting safety training.
b. Written résumés showing not less than one year of acceptable experience with explosives under a qualified licensed blaster.
3. At least 5 days prior to any blasting, the Contractor shall submit a blasting plan to the CWD or its
representative and all other applicable permitting authorities. The blasting plan shall at a minimum include the following items:
a. A description and license number of the vehicle to be used for transportation of explosives, routes to be traveled and proposed hours of travel, and qualifications of driver.
b. Type of explosives, initiation system, drilling system, loading plan, firing plan, pre- blast and post-blast inspection, handling of misfires, and removal and disposal of excess explosives.
c. Proposed signs, guard system, signal system, methods of communication, pre- blast notification of affected agencies or entities and traffic control measures during blasting.
d. Copies of all required permits and licenses.
4. The safety of personnel shall be the primary consideration in decisions involving the use of explosives. Protection of vehicles, utilities, and adjacent property from ground motion or fly-rock must also be provided. Use of blasting mats and other protective devices will be required. The Contractor shall retain sole responsibility for repairing or replacing any utilities or property damaged because of his blasting operations. Due to the proximity of residences and vehicular traffic, use of controlled blasting techniques is specifically required. A delayed blasting system shall be utilized that will not allow more than two holes to detonate simultaneously. Blasting will only be allowed during times of low traffic on the adjacent roads and only in conjunction with traffic closure for the period during which blasting occurs. The appropriate jurisdictional authority must approve traffic closure.
closure for the period during which blasting occurs. The appropriate jurisdictional authority must approve traffic closure.
102.13 STOCKPILING EXCAVATED MATERIAL
Excavated material shall be piled in locations that will not endanger the work, create traffic hazards, or obstruct sidewalks and driveways. Fire hydrants, valve boxes, manholes and other utility access points shall be left unobstructed until the work is complete. Gutters and other water courses shall not be obstructed unless other satisfactory provisions are made for runoff and street drainage.
All surplus material and excavated material unsuitable for backfilling shall be removed from the site and disposed of in areas secured by the Contractor.
102.14 DEWATERING TRENCHES
No groundwater dewatering operation shall begin until a Construction Dewatering Permit has been obtained by the Contractor from the Colorado Department of Health and Environment (CDPHE). The dewatering permit may be waived when 100 percent of the groundwater removed from the excavation is used for onsite dust control or other land application approved by the CDPHE.
In addition to a Construction Discharge Permit, no groundwater shall be discharged to a street, storm drainage system, drainage ditch, irrigation ditch, pipe or other facility without written permission from the owner of the receiving facility. Under no circumstances shall the trench water be discharged into sanitary sewers.
Trenches shall be kept free of water during pipe laying operations. The water level shall be maintained at least six (6) inches below the trench bottom throughout the placement of bedding, pipe laying, joining and backfilling operations. The dewatering shall be carried out so that it does not destroy or weaken the strength of the soil under or along the side of the trench. Watertight plugs shall be installed in the ends of all water lines when the trench is not being dewatered. Surface water from any source shall be prevented from entering the trench excavation. No additional payment will be made to the Contractor due to an unstable trench or pipe foundation conditions caused by surface water entering the trench.
102.15 BACKFILLING PIPE AND STRUCTURES
Unless otherwise specified or approved by CWD, all backfill material shall be placed with moisture-density control in accordance with the typical trench detail shown on the Standard Detail Sheets. All approved backfill material shall be adjusted to within three (3) percent of the optimum moisture content prior to its placement in the trench. Jetting or water soaking trenches to achieve compaction of the backfill will not be permitted except when the backfill consists of gravel or other granular material having less than 20 percent of weight passing a No. 200 sieve and a geotechnical investigation has determined that expansive in-situ materials are not present.
During initial backfilling, the Contractor shall take all necessary precautions to prevent movement or distortion
of the pipe or structure being backfilled. Pipe haunching material shall be placed and compacted in even lifts on both sides of the pipe to six (6) inches above the top of the pipe. Above the bedding and haunching material, earth backfill material shall be placed full width in uniform layers not more than twelve (12) inches thick. Each layer shall be compacted to the required density with approved mechanical or hand tamping equipment.
All backfill shall be frequently tested to ensure that the required density is being attained. The minimum requirements for compaction testing shall be as follows:
For every 400 lineal feet of trench and each branch or section of trench less than 400 feet in length, at least one compaction test shall be performed for each two-foot vertical lift of backfill material placed. The first test shall be taken approximately two feet above the top of pipe and the last test shall be at the pavement subgrade or six inches below the ground surface in unpaved areas. Compaction tests shall be taken at random locations along the trench and wherever poor compaction is suspected. If any portion of the backfill placed fails to meet the minimum density specified, the area shall be defined by additional tests if necessary and the material in the designated area shall be removed and replaced to the required density at the Contractor’s expense.
All compaction testing shall be performed by a qualified representative or an independent soil testing laboratory. The Contractor shall bear the cost of testing. It shall be the Contractor’s responsibility to make necessary excavations to accommodate compaction tests at all locations designated.
A summary report of all compaction test results shall be submitted to CWD. The test results are required as a basis of acceptance of facilities. (See Section 107.)
Concrete structures shall not be backfilled until the concrete and mortar therein has attained a minimum compressive strength of 2000 psi and can sufficiently support the loads imposed by the backfill. Select backfill shall be placed simultaneously on all sides of the structure in layers approximately twelve (12) inches thick. Each layer shall be compacted to not less than ninety-five (95) percent of the maximum dry density determined in accordance with AASHTO T-99.
102.16 GRANULAR STABILIZATION, BEDDING AND HAUNCHING MATERIALS
When granular materials are required for stabilization of poor subgrade soils, bedding of pipe and structures, and haunching around pipe it shall meet the following graduation requirements.
Percent by Weight Passing Square Mesh Sieves
Sieve Size | Pipe Bedding & Haunching Material | Granular Stabilization Material (Screened or Crushed Rock) | Pit Run Aggregate |
---|---|---|---|
8 inch | --- | --- | 100 |
2 inch | --- | 100 | --- |
1 inch | 100 | --- | --- |
No. 200 | 20 Max. | 20 Max | 20 Max |
102.17 RESTORATION OF GROUNDS
The cleanup and restoration of grounds shall be a continuous process from the beginning of construction to final completion of the work. The Contractor shall keep the work site free from accumulation of debris and waste material caused by his operation.
Immediately after the pipeline is backfilled, the area shall be cleaned and restored to the original grade and condition. All fences, utilities, culverts, ditches, structures, grassed areas and plantings shall be replaced and restored to a condition equal to or better than that at the beginning of construction.
102.18 RESTORATION OF PAVED SURFACES IN SITUATIONS WHERE EXISTING ROADWAYS ARE TO BE KEPT IN SERVICE
Immediately after any section of a completed pipeline has been tested and approved by CWD, the Contractor shall replace all paved surfaces removed or damaged by his operation. All pavement replacement shall be in accordance with the typical trench detail shown on the standard detail sheets, and in accordance with any permit requirements imposed by the City, County, or State.
Unless otherwise approved, all asphalt pavement removed shall be replaced with hot mixed bituminous pavement in accordance with Colorado Division of Highways. All road base shall be Colorado Division of Highways, Class 6, Aggregate Base Course. Paved surfaces shall be restored to their original line and grade and finished to match adjacent undisturbed surfaces.
All curbs, gutters, sidewalks, gutter pans, concrete driveways, concrete pavement, and other concrete hardscape within the right of way shall be replaced by a qualified concrete contractor with a permit issued by the Office of the County Engineer. All concrete shall be Colorado Division of Highways, Class B.
102.19 EROSION CONTROL
Erosion control measures shall be constructed, installed, maintained, moved (if needed) and removed in accordance with the project Storm Water Management Plan (SWMP), the CDPHE Construction Permit (if any) and Section 208 of the CDOT Standard Specifications for Road and Bridge Construction. Erosion control measures shall be maintained during the life of the Contract to prevent or minimize erosion, sedimentation, and pollution of any state waters and wetlands.
103.1 INSTALLATION OF PIPE AND APPURTENANCES
All pipe, valves, hydrants, manholes and other pipeline appurtenances shall be installed and tested in accordance with the construction plans and specifications, applicable AWWA, ASTM, or AASHTO Standards and Manufacturer’s instructions. When installation instructions or procedures differ, the CWD inspector will determine which will take precedence over the others.
103.2 PIPE LAYING
Pipe shall be laid on the alignment shown on the plans or staked. Unless otherwise specified or approved, all pipelines shall be laid to a minimum depth of fifty-four (54) inches measured from the finished grade to the top of pipe. Watermain pipe shall be installed on the north and east sides of the right of way in accordance with the CWD standard details.
The inside of the pipe and jointing surfaces shall be kept clean and free from mud, dirt, gravel, ground water, and other foreign material. When pipe laying is not in progress, the open ends of the pipeline shall be kept closed with watertight plugs.
Long radius horizontal or vertical curves may be laid with standard pipe by deflections at the joints of rigid pipe or by deflecting the entire length of flexible pipe.
Maximum deflections for PVC C900 pipe for 20’ pipe lengths and diameters equal to or less than 12” shall be 0.48’ feet per pipe length or 1.2 degrees with a minim allowable radius of 820 feet.
Maximum deflections at pipe joints for diameter pipe greater than 12” or other materials shall be per the Manufacturer’s recommendations or applicable AWWA Standard.
All ductile iron pipe with push on type joints shall be electrically connected with cadweld connectors and No. 10 copper wire or a minimum of two brass wedges installed at each joint. The wire ends and cadwelds shall be sealed to prevent corrosion.
When installing piping on a grade of 15% or steeper, the bells shall face uphill.
The design Engineer shall provide a pipe anchorage design and consider slope stability when piping is to be installed on a grade of 20% or steeper.
103.3 INSTALLATION OF TRACING WIRE
All nonmetallic pipe shall be buried with a continuous electrical tracing wire to enable future location of the pipe. Tracing wire shall be taped to the top of the pipe at 10-foot intervals with 2” wide PVC tape to prevent dislocation of the wire during backfilling. At all fire hydrants, valves, and other locations shown on the plans, the tracing wire shall be extended to the ground surface for easy access. In paved areas, the tracing wire shall be brought upon the inside of the valve box and securely fastened to the inside wall within 4 inches from the top of the lid. Splices for tracing wire shall consist of a wire nut completely encased with TBT-20 rubber tape.
103.4 POLYETHYLENE ENCASEMENT
Prior to backfilling, all cast iron and ductile iron pipe, fittings, valves, and other metal pipe and appurtenances shall be wrapped with polyethylene encasement material. The polyethylene encasement shall be a minimum thickness of 0.008 inches (8 mil). Installation of the polyethylene tube shall be in accordance with one of the methods described in AWWA C-105.
Ductile iron valves and fittings shall be fully encapsulated by the polyethylene sheeting except for the valve operating nut. The ends of the polyethylene sheeting shall be taped around the full circumference of the pipe. All splices shall overlap a minimum of 12” and the full length of the seam shall be taped.
103.5 THRUST RESTRAINT
Thrust restraint shall be provided at all pipe bends, tees, caps, valves, hydrants and other locations shown on the plans. The thrust restraint may be provided by concrete blocking or mechanical joint restraint. If mechanical joint restraint is used in lieu of concrete blocking, the minimum distance for joint restraint along the pipe away from the fitting shall be determined using the EBAA Iron Thrust Restraint calculations per the Restrain Length Calculator located at: http://rcp.ebaa.com/
Joints for all fittings and valves shall have mechanical connections per CWD Material Specifications.
103.6 CONCRETE BLOCKING
The size and location of blocking shall be as shown on the plans, and as directed by CWD. Thrust blocks shall be poured on firm, stable foundation material and all bearing surfaces shall be against undisturbed earth. Form work shall be provided as needed to ensure access to all bolts, nuts, and fittings for repair after placement of the concrete. Plastic sheeting shall be placed between the concrete and the fitting, valve, or piping and the concrete shall not extend around more than one-half of the circumference of the fitting or pipe at any point.
Concrete for support and thrust blocks shall be made with Type II Portland Cement and shall reach a minimum compressive strength of 3000 psi in 28 days.
Reinforcing steel and bolts used to anchor valves, fittings, etc., to thrust blocks when required shall meet tensile requirements of ASTM Grade 40. All anchorage steel not embedded in concrete shall be coated with coal tar or be Cor-Ten steel.
Thrust blocking for bends or pipes greater than 12-inch in diameter or in areas where the operating pressure is greater than 125 psi are not covered by the Standard Details and require special consideration by the design Engineer.
103.7 INSTALLATION OF VALVES AND VALVE BOXES
Each valve shall be installed in a vertical position with a suitable support block as shown on the Standard Water Line Detail Sheet. An adjustable slip type valve box shall be set into position during backfilling operations. The lower section of the valve box shall be supported with brick or block so that it does not rest directly upon the body of the valve or upon the water main. The upper section of the unit shall be placed in proper alignment and adjusted so that its top will be at final grade upon completion of surfacing. The completed valve box shall be vertically centered over the valve operating nut and each valve shall be tested for proper access and operation.
103.8 INSTALLATION OF FIRE HYDRANTS
Hydrants shall be installed at the locations shown on the plans and in accordance with the standard details. They shall be plumb and the center of the pumper nozzle shall be no less than eighteen (18) inches and no more than twenty-two (22) inches above finished grade and set on precast concrete blocks. A minimum of ¼ cubic yard of washed ¾ inch gravel shall be placed around the base of the hydrant to insure proper drainage of the hydrant after use. Blocking of the hydrant shall consist of pouring a solid concrete base of not less than ¼ cubic yard extending from the hydrant base to the undisturbed soil on the bottom and sides of the trench. The thrust block shall be formed in order to not prohibit full access to all bolts and nuts, and to not block the barrel drain weep holes.
All pipe and fittings from the fire hydrant to the main water line shall be mechanically restrained. The mainline tee shall be mechanically restrained and a concrete thrust block poured behind it.
Weep holes which drain the hydrant shall not be covered with concrete.
103.9 INSTALLATION OF WATER SERVICE PIPE
Water service pipe shall be laid not less than ten (10) feet horizontally from any potential source of contamination (both service and collection lines). Where a 10-foot horizontal separation is not possible, the service line shall be at least eighteen (18) inches above the top of the sewer line and with a minimum cover of forty-two (42) inches. If placed in a common trench with the sewer service, the water service must be placed on a solid shelf excavated to one side of the trench. Where the 18" separation is not practical, the sewer line must be encased in a casing pipe or constructed with C-900 PVC pipe.
Connecting water services that are less than or equal to 1-1/2” diameter to distribution lines that are under pressure at the time the service connection is made shall include a double strap brass tapping saddle and CC threaded corporation stop.
When installing water services less than or equal to 1-1/2” diameter in conjunction with the installation of the water main, and the service connections are to be made prior to pressurizing the new main, the connections shall be made through a brass corporation stop threaded into a tap tee.
The main shall be tapped at 45 degrees off the vertical (approximately 2 o’clock or 10 o’clock), and the stop must be turned so the T-handle of the corporation valve will be on top. A “gooseneck” loop shall be set vertical immediately after the corporation stop (6" to 12" in height) in the copper service line.
Water services equal to or larger than 2” shall include a gate valve and tapping sleeve if made while the main is under pressure, or gate valve and tee if the main is not under pressure.
Service lines shall be installed to the meter pit location shown on the plans or as designated by CWD. Wherever physical conditions permit, the meter pit shall be located within the adjacent road right of way. Meter pits shall not be placed under curb, gutter, sidewalk, or driveways.
Taps 1-1/2” and less shall be spaced at least 18” apart. Taps greater than 1-1/2” shall be spaced a minimum of 36” apart.
103.10 SERVICE STUBOUTS
The service line shall extend to the meter pit location shown on the plans or designated by CWD. The Contractor shall install the meter yoke and pit so that the final grade elevation will be above the final grade by 0.2 feet. Customer service line stubouts are the responsibility of the owner and not the CWD.
The service line shall extend to the back of the multipurpose or utility easement and marked either by a 4"x 4" board or steel fence post buried vertically. The board or post shall extend 3 feet above the ground surface with the exposed portion painted blue. The end of the service line shall be capped with watertight a plug.
103.11 SYSTEM-PROTECTION DEVICES
Appropriate backflow prevention devices shall be required on any connection to the system which utilizes irrigation systems, fire protection sprinkler systems or presents the possibility of backflow or siphonage. All backflow prevention devices shall be installed in accordance with the most current version of the international plumbing code and the manufacturers recommendations. Backflow prevention will be at the total expense of the customer, will be installed on the customer’s side of the meter, and will be subject to testing and inspection as required by the Colorado Department of Public Health and Environment and CWD.
103.12 MAINLINE CONNECTIONS TO EXISTING MAINS
New water lines shall not be placed in service until the new lines have been tested and disinfected by the Contractor and inspected by CWD. CWD technicians shall perform bacteriological testing prior to placing the new line in normal service. If test results fail, the Contractor shall re-disinfect the lines as directed by CWD. All costs for disinfection and re-disinfection of lines shall be the responsibility of the Contractor.
Where the connection of the new work to old requires interruption of service, CWD and the Contractor shall mutually agree upon a date and time for connections which will allow ample time to assemble labor and materials. The Contractor, in conjunction with the CWD project representative, shall notify all water users affected in accordance with CWD’s Specifications.
103.13 INSTALLATION OF SAMPLE STATIONS
The sample station shall be located within the Public Right of Way or Utility Easement. The setback shall be such that the station is as close to the curb and/or sidewalk as possible. The bottom of the station shall be level with the final grade of adjacent curb or sidewalk.
The sample station shall be installed with a brass tapping saddle and corporation stop at the main, similar to a standard service tap connection. The service line shall be 3/4 inch, type “K” copper tubing. In no case will the service line be more than 50 feet in total length. Just prior to the sample station, a brass curb stop shall be installed to provide a means of isolating the station for maintenance or repairs. The station shall not be located in a fenced or restricted access area, nor shall it be painted or altered in any way.
103.14 SEPERATION BETWEEN WATER LINES AND SOURCES OF CONTAMINATION
103.14.1 PARALLEL INSTALLATION
Watermains must be at least 10 feet horizontally from any existing or proposed non-potable pipe such as a gravity sanitary or storm sewer, raw surface water pipe, irrigation line, grey water, liquid petroleum, septic tanks, or subsoil treatment system. The distance is measured horizontally from inside pipe edge to inside pipe edge.
Exception
When it is impractical to maintain the 10’ horizontal separation the following installation method may be used:
a. Place the water line in a separate trench or on a separate shelf in the same trench with the bottom of the water line at least 18” above the top of the non-potable pipe and construct the non-potable pipe with 150 psi rated water main quality pipe meeting AWWA standards for potable pressure piping.
b. Other solutions presented by the Colorado registered professional engineer design engineer will be considered.
Approval from the owner of the non-potable pipe must be obtained prior to any modification or encasement of the piping
103.14.2 CROSSING
Watermains crossing any existing or proposed non-potable pipe such as a gravity sanitary or storm sewer, raw surface water pipe, grey water, liquid petroleum, septic tanks, or subsoil treatment system must have a minimum of 18” of clear space between the outside of each pipe. At the crossing, one full length of watermain piping must be centered on the crossing so that the joints are as far from the non-potable pipe as possible.
Exception
When it is impractical to maintain the 1.5’ vertical separation one of following installation methods may be used:
a. Place the non-potable pipe in a watertight casing a minimum of 9’ from each side of the watermain. The casing shall be 150 psi rated water main quality pipe meeting AWWA standards for potable pressure piping and shall include casing spacers and end seals. If the space between the casing pipe and the watermain is less than 6” rigid foam installation shall be placed between the two pipes. The foam installation must be installed so that it fits tightly between the pipes.
b. Encase the non-potable pipe in concrete a minimum of 10’ from either side of the crossing.
c. Other solutions presented by the Colorado registered professional engineer design engineer will be considered.
In all cases, suitable backfill or other structural protection shall be provided to preclude the settling or failure of both pipes.
Crossings of sewer and water lines shall not be at an angle less than 45 degrees nor shall a sewer line or water line be installed within 10 feet of each other unless approved by the CWD.
Approval from the owner of the non-potable pipe must be obtained prior to any modification or encasement of the piping
103.15 EARTH BACKFILL MATERIAL
Under normal conditions, native material shall be used for bedding, haunching and backfilling. Earth backfill material shall consist of approved materials developed from project excavations or imported from another source. To be suitable for backfill, earth or earth and rock material shall be free from muck, frozen lumps, chunks of concrete, ashes, trash, vegetation, and other debris.
All shall have a plasticity limit of less than 7%. All excavated materials which, in the opinion of CWD, are unsuitable for use in the backfill shall be removed from the site and disposed of by the Contractor at his expense. The maximum size of rock or clod allowed in the various backfill zones shall be as follows:
Zone of Backfill | Maximum size of rock of clod in backfill measured in greatest dimension |
---|---|
Trench backfill from a horizontal plane 6" above top of pipe to ground surface or subgrade of road base course | 8" |
Within 6” of the exterior surface of pipe or structure | 1 1/2" |
104.1 GENERAL
The contractor shall furnish all labor, equipment, tools, materials, water and other incidental items required to conduct all testing, flushing, disinfection required per these specifications. All pressure and leakage testing, and disinfection shall be performed by the Contractor under direct supervision of the CWD in accordance with AWWA C605-21, AWWA Manual of Practice M23, CDPHE requirements, the specifications contained herein, and as directed by the CWD.
The testing sequence shall be as follows:
- Fill and pressurize the main to at least the static pressure of the existing system to be connected to.
- Perform a thorough flush of the new system obtaining a minimum of 3 feet per second velocity in all pipe sections. If possible flush from two directions.
- Disinfect the new piping and appurtenances and perform a final flush.
- Following chlorination, all treated water shall be thoroughly flushed from the newly laid pipe at its extremity until the replacement water throughout its length has a residual free chlorine level not greater than the residual normally found in the system.
- Perform a pressure and leakage test.
- Conduct a bacteriological test.
104.2 BACKFLOW PROTECTION
When existing water mains are used to supply water for flushing and testing, they shall be protected from backflow contamination by temporarily installing a double check valve backflow prevention assembly between the test and supply water mains. Backflow prevention assemblies shall be tested and certified before use in accordance with CWD requirements. Before the hydrostatic testing, the temporary backflow device shall be removed and the section of piping to be tested isolated from the supply system.
104.3 DISINFECTION OF WATER LINES
After completion of pressure and leakage testing and prior to being placed into service, all new water mains and repaired portions of or extensions of existing mains shall be chlorinated by the Contractor in accordance with AWWA Standard C-651-14 and as modified herein.
104.4 INITIAL FLUSHING OF POTABLE WATER MAINS
Sections of pipe to be disinfected shall first be flushed to remove any solids or contaminated material that may have entered the pipe. The duration of flushing shall be long enough to ensure a minimum of three changes of water pass through the new piping. If no hydrant is installed at the end of the main, then the proper size and quantity of taps or a temporary hydrant shall be installed to flush the line at a minimum velocity of 3 feet per second in accordance with the below table:
Table 104.1
Required flow and openings required to flush pipelines at 3.0 ft/sec
Pipe Dia. (inches) | Flow required for 3.0 ft Velocity in Main (gpm) | Size of Tap 1" | Size of Tap 1-1/2" | Size of Tap 2" | Number of Hydrant Outlets 2-1/2" | Number of Hydrant Outlets 4-1/2" |
---|---|---|---|---|---|---|
4" | 120 | 1 | - | - | 1 | 1 |
6" | 260 | - | 1 | - | 1 | 1 |
8" | 470 | - | 2 | - | 1 | 1 |
10" | 730 | - | 3 | 2 | 1 | 1 |
12" | 1060 | - | - | 3 | 2 | 1 |
16" | 1880 | - | - | 5 | 2 | 1 |
104.5 CHLORINE APPLICATION
All new water lines shall be disinfected by introducing chlorinated water into the new piping so that an initial chlorine concentration of 50 ppm is obtained. A water truck or other means approved by the CWD shall be used to introduce chlorinated water into the new piping.
The disinfection solution shall consist of sodium hypochlorite as provided by the Clifton Water District. An adequate amount of chlorine shall be mixed with clean water to obtain a minimum chlorine residual of 100 ppm at all points within the new piping, including all branches, fire hydrants, and stubs and dead ends.
104.6 POINT OF APPLICATION
At a point as close as possible to, but no farther than 10 feet down stream of the beginning of the new pipeline chlorine shall be introduced into the pipeline via a corporation tap and copper whip. Alternate points of application may be used when approved or directed by CWD.
104.7 PREVENTING REVERSE FLOW
Valves shall be manipulated so that the strong chlorine solution in the line being treated will not flow back into the line supplying the water. Check valves may be used if pre-approved by CWD.
104.8 RETENTION PERIOD
Chlorinated water shall be retained in the pipe at least twenty-four (24) hours. After this period, the chlorine residual at pipe extremities and at other representative points shall be at least ten (10) mg/l.
104.9 CHLORINATING VALVES AND HYDRANTS
In the process of chlorinating newly laid pipe, all valves or other appurtenances shall be operated while the pipeline is filled with the chlorinating agent and under normal operating pressure.
104.10 FINAL FLUSHING AND TESTING
Following chlorination, all treated water shall be thoroughly flushed from the newly laid pipe at its extremity until the replacement water throughout its length has a residual free chlorine level not greater than the residual normally found in the system.
104.11 BACTERIOLOGICAL TEST
After the final flush, the CWD will take two consecutive sets of samples taken at least 24 hours apart for laboratory analysis. At least one sample shall be taken from each branch for each set of samples and on sample every 1000 feet along the mainline. If the test fails, the Contractor will re-chlorinate according to the Standard and retest. This sequencing shall continue until the bacteriological test passes. Only upon a successful bacteriological test will the installation of service connections and or meters be approved. All costs associated with testing, flushing, and disinfecting shall be the responsibility of the Contractor.
104.12 PRESSURE TESTING
No pressure testing shall be performed until all thrust blocks have been placed and cured for at least seven (7) days, and the pipeline backfilled adequately to prevent any movement or lifting of the pipe. Pavement or other permanent surface shall not be placed until all pressure and leakage tests are satisfactorily completed. No testing shall be considered completed unless a CWD representative is present to witness the testing.
104.13 TEST PRESSURE
Unless otherwise specified, the test pressure for all pipes shall be 1.25 times the normal operating pressure at the lowest point in the piping, or 1.5 times the normal operating pressure at the highest point in the piping, or 150 psi, which ever pressure is greatest. In no case shall the test pressure exceed the rated pressure for the piping, valves, or fittings.
104.14 FILLING
The pipeline shall be filled with potable water at least twenty-four (24) hours before being subjected to the hydrostatic pressure test. Each section of the pipeline shall be filled slowly and from the lowest point in the pipe section. All air shall be expelled by means of taps, fire hydrants, or air release valves at points of highest elevation.
104.15 PROCEDURE
The test shall be performed only after the pipeline has been properly filled, flushed, purged of air. The specified test pressure shall be applied by means of a pump connected to the pipe in a manner satisfactory to CWD. The test duration shall be a minimum of 2 hours.
The testing allowance shall be defined as the allowed quantity of makeup water supplied to the pipe section during the test to maintain a pressure within 5 psi of the required test pressure. No pipe installation will be accepted if the leakage for the section of line being tested is more than the rate calculated using the following formula:
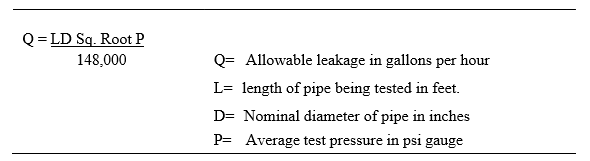
Leakage is defined as the quantity of water to be supplied to the section of pipeline being tested, which is necessary to maintain the specified leakage test pressure after the pipe has been filled with water and the air expelled.
Request More Information:
If you have any questions, or comments or would like a PDF version of this information please fill out the form below.